WestRock : un projet, trois dangers éliminés !

Sur la photo, Mathieu Côté-Genest, gestionnaire du projet.
WestRock est une entreprise qui se spécialise dans la production de carton et d’emballage. L’usine de Sainte-Marie, anciennement RockTenn, a été fondée en 1977 et est devenue une filiale de la compagnie WestRock en 2015. L’usine de 225 employés produit des emballages de carton principalement pour le secteur alimentaire.
Le projet a débuté en septembre 2018, à la suite de deux événements : un travailleur a fait une chute de plain-pied en transportant un baril vers la benne à déchets et un travailleur a presque chuté dans la benne en vidant le contenu d’un baril. Les résultats des enquêtes et analyses d’accidents ont débouché sur un projet d’amélioration chapeauté par Mathieu Genest-Côté.
Situation en 2018
Auparavant, les travailleurs devaient déplacer un baril contentant des rebuts, essentiellement de carton ou de papiers, pour vider son contenu dans une benne à déchets qui se trouvait sur une plateforme à l’extérieur. Pour se faire, il devait traverser l’entrepôt où cohabitent des chariots élévateurs. Les travailleurs étaient donc exposés à des risques de collision. Sur la plateforme, ils étaient exposés à un risque de chute dans la benne et à une chute de même niveau particulièrement en saison hivernale. Les travailleurs devaient également soulever manuellement les barils pour les vider.
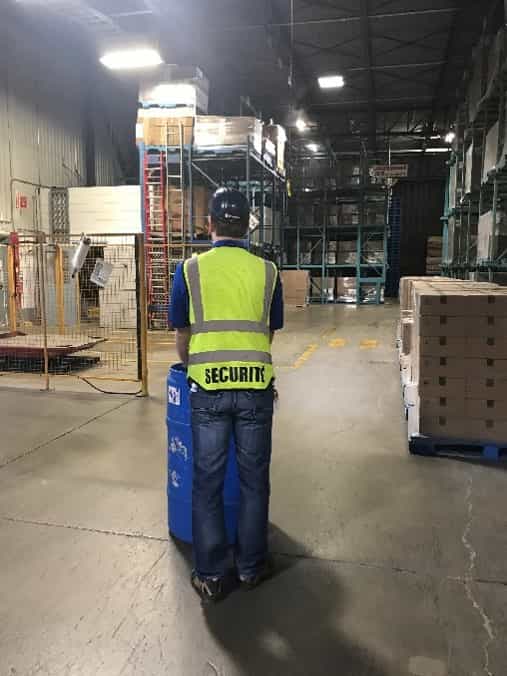
Travailleur transportant un baril avant l’innovation
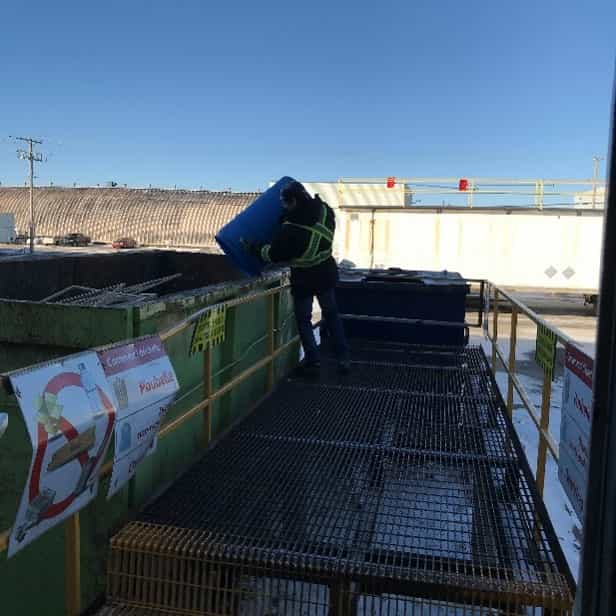
Travailleur sur la passerelle vidant le baril avant l’innovation
Situation actuelle
La benne se trouvant à l’extérieur a été remplacée par un compacteur automatisé installé dans une salle prévue à cet effet, à l’intérieur, près des lieux de production. Les travailleurs n’ont donc plus à traverser l’entrepôt et à s’exposer à un risque de collision avec un chariot élévateur. Les barils qui contenaient les rebuts ont été remplacés par des conteneurs sur roulettes. Lorsque le conteneur est plein et que son contenu doit être vidé, les employés se déplacent dans la salle prévue à cet effet. Le conteneur est installé sur un dispositif qui videra son contenu mécaniquement. Ensuite, le travailleur quitte la salle, ferme la porte et enclenche le bouton qui manipule le conteneur pour le vider dans le compacteur. La personne n’a donc plus à soulever le conteneur et la sécurité mise en place assure qu’elle n’est exposée à aucun danger lorsque le conteneur se transvide.
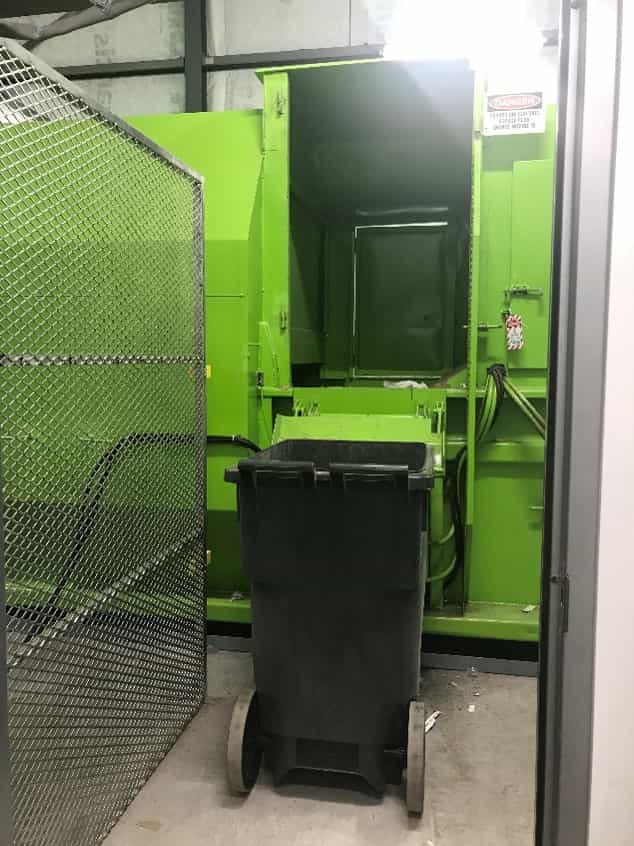
Compacteur automatisé
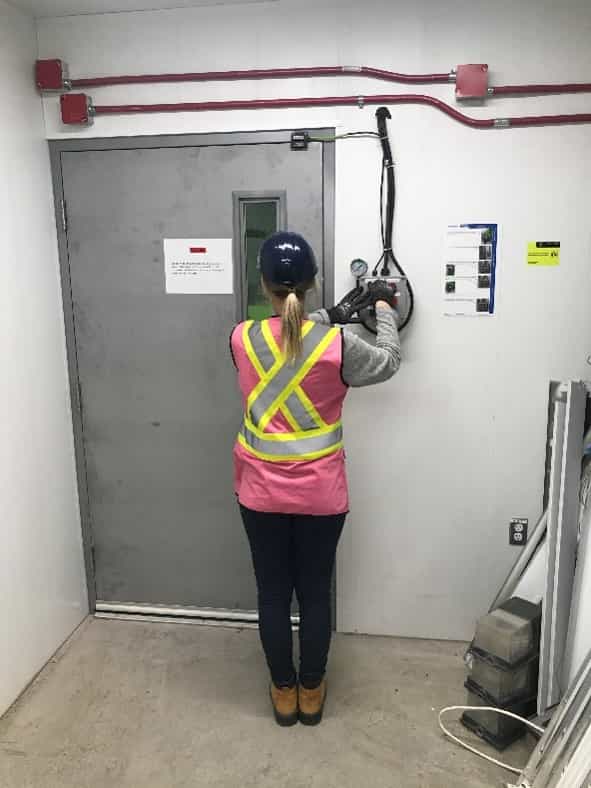
Travailleuse qui active le déversement dans le compacteur
Caroline Lavoie, coordonnatrice santé et sécurité, chez WestRock souligne que l’innovation est en place depuis décembre 2019 et qu’aucun événement n’est survenu en lien avec cette tâche. Tous les dangers et les risques liés à son exécution ont été considérés. Il n’y a plus de cohabitation entre les piétons et les chariots, les travailleurs n’ont plus à se déplacer sur la passerelle et ne peuvent plus chuter, les travailleurs n’ont plus à soulever de charge dans l’exécution de la tâche. Elle rappelle que pour WestRock, la prévention des risques engendrés par la cohabitation entre les chariots élévateurs et les piétons est une priorité.
Vous aimeriez partager une innovation que vous avez mise en place dans votre entreprise, écrivez-nous : pratiquesrh@fccq.com